circular M
Expert in production & manufacturing
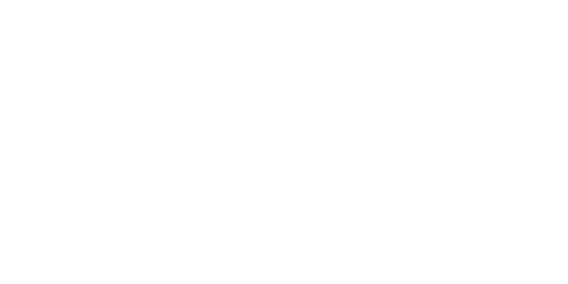
PARTNERSHIP FOR
THE BEST SOLUTION
MIDI Line – technologically advanced and expertly crafted
Akkodis´s process and technology leadership with circular M´s mastery of development and production, resulting in a product that is both high-quality and cutting-edge. If you´re seeking top-of-the-line equipment, the MIDI Line is sure to exceed your expectations.
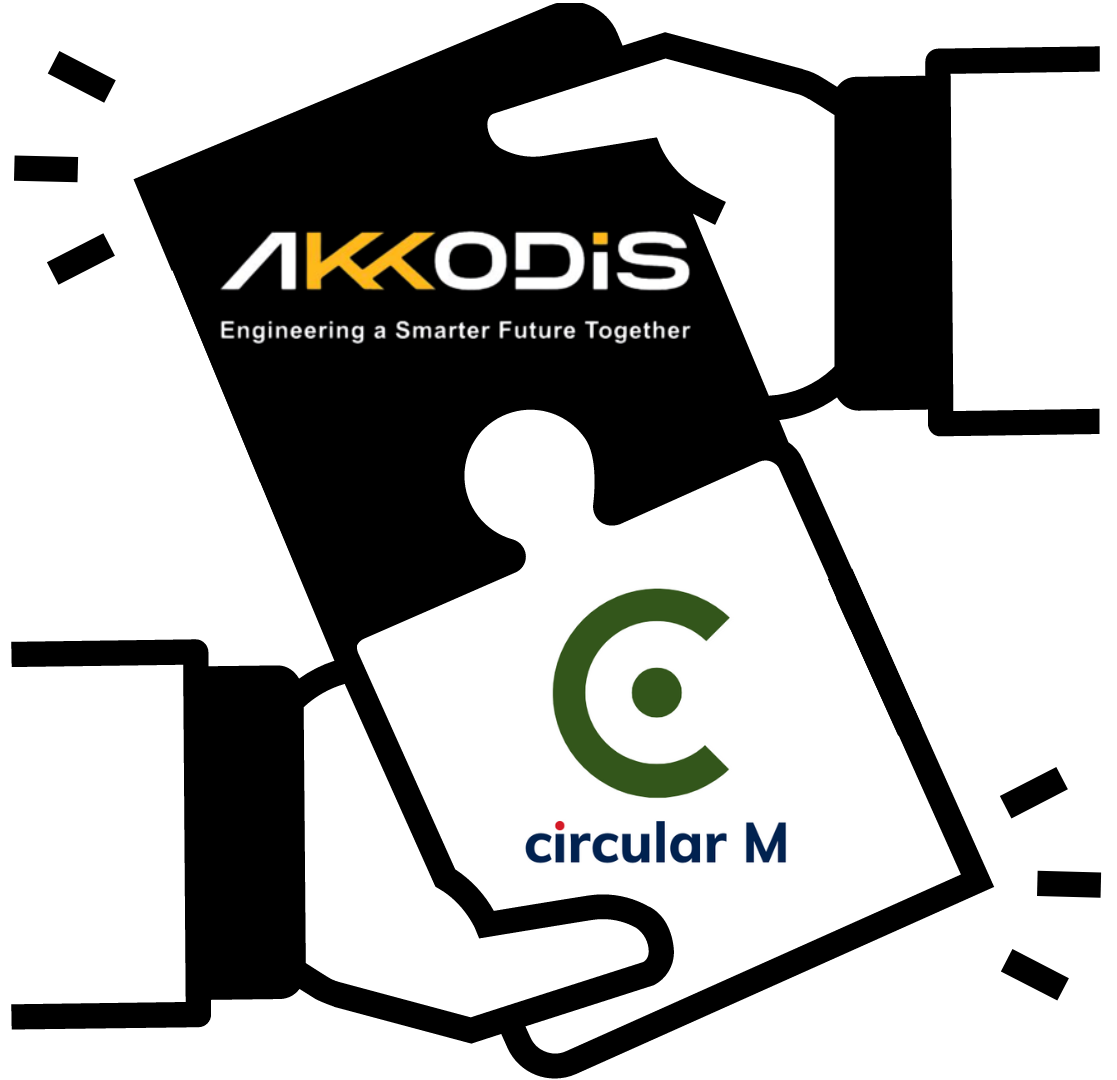
Together, these two companies can leverage their strengths to achieve unparalleled success in the field of kiln technology and chemical processes. Company A’s extensive knowledge and experience, combined with Company B’s expertise in production and manufacturing, make them a formidable partnership in this industry.
MIDI Line Technology
Process thermally splits materials into gas and solid fractions. The material is heated to between 500 and 1100 degrees Celsius in a rotary kiln, and the fractions are separated in the outlet housing. The solid fraction is further separated into different liquid fractions through a multi-stage condensation process and collected in external tanks. The non-condensable gases produced during the process can be used to generate electricity in a micro gas turbine (CHP), supplied to other processes, or recycled back into the thermolysis process.
- Fully automatic control system
- Man-free operation possible
- State of the art technology for rotary kilns
- Electrical heated for minimum of energy losses & stable process conditions
- Combinable with green power (wind, solar, water)
- Liquid output is in high quality and flexible range
- Solid output is usable (middle to high price carbon)
- Designed for continuous processing 24h/7d
- Standard operation of 7,500 hours per year
- Noise-reduced design
- Operation temperature up to 800°C – need for less Sulphur content
- Leakage proof design
- Safety analysis (HAZID/HAZOP)
- Operation compliant with EUenvironmental & risk regulations
- Ready assembled and tested module containers
- Simply & quick assembly on customers site
- Standard 40″ HC conatier for simple transport
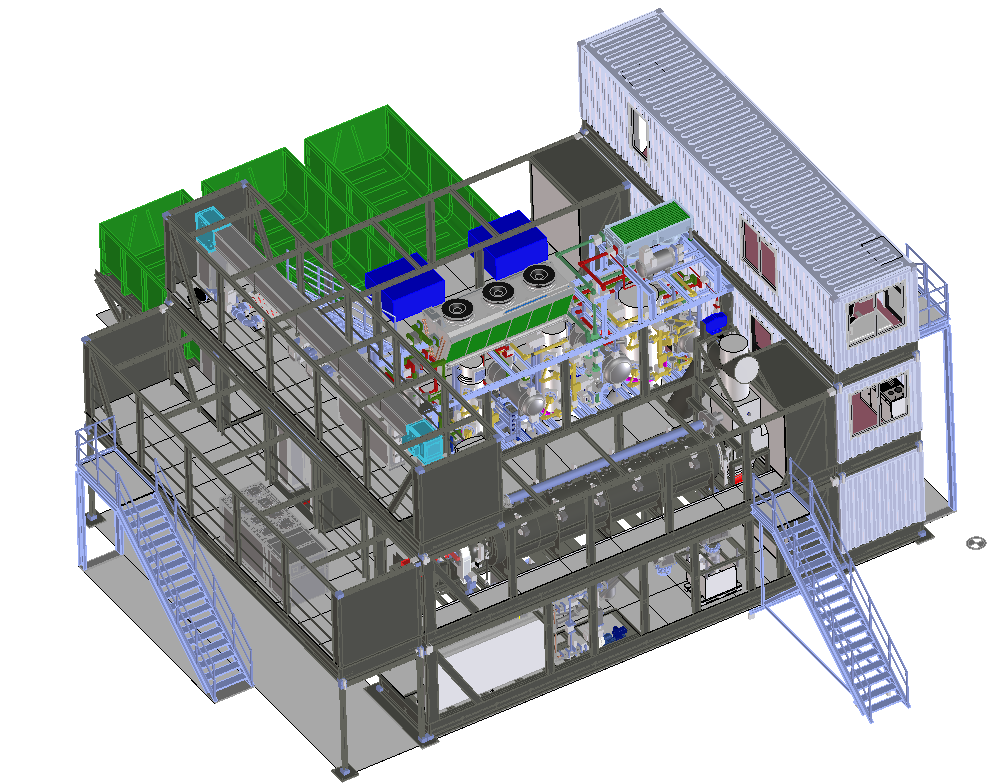
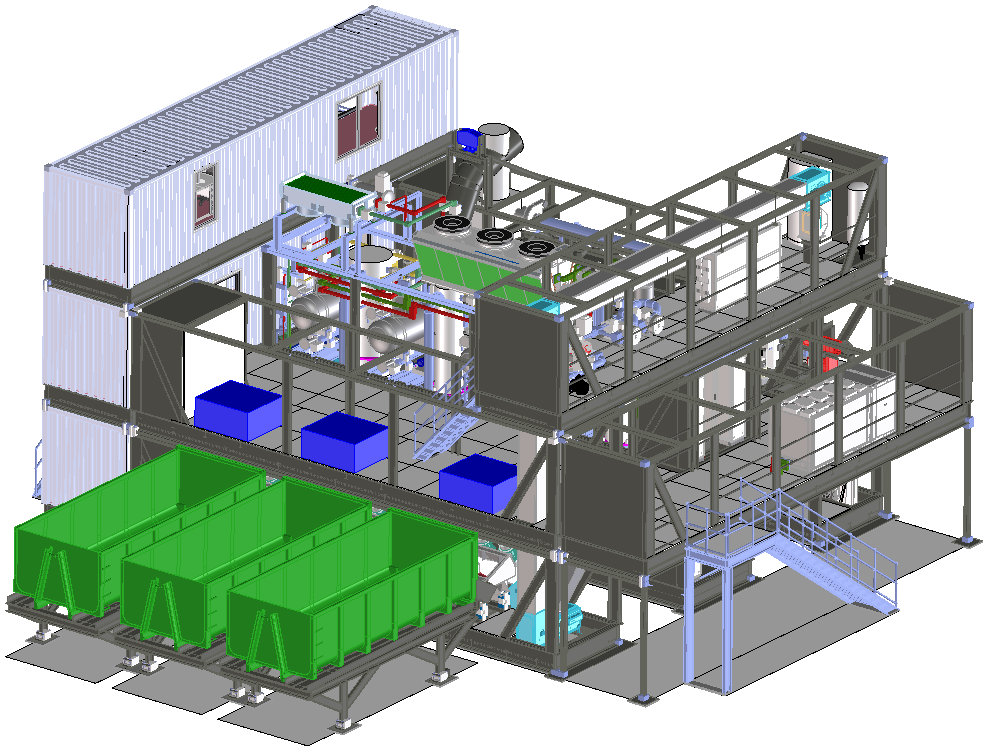
circular M
Your expert in production & manufacturing
- New process in electroplating technology
- No „shadows“ in the process
- Significant process time optimization
- Over 86% space optimization
- No fumes (are intercepted)
- Significant cost savings
- Modular design allows for easier maintenance and replacement
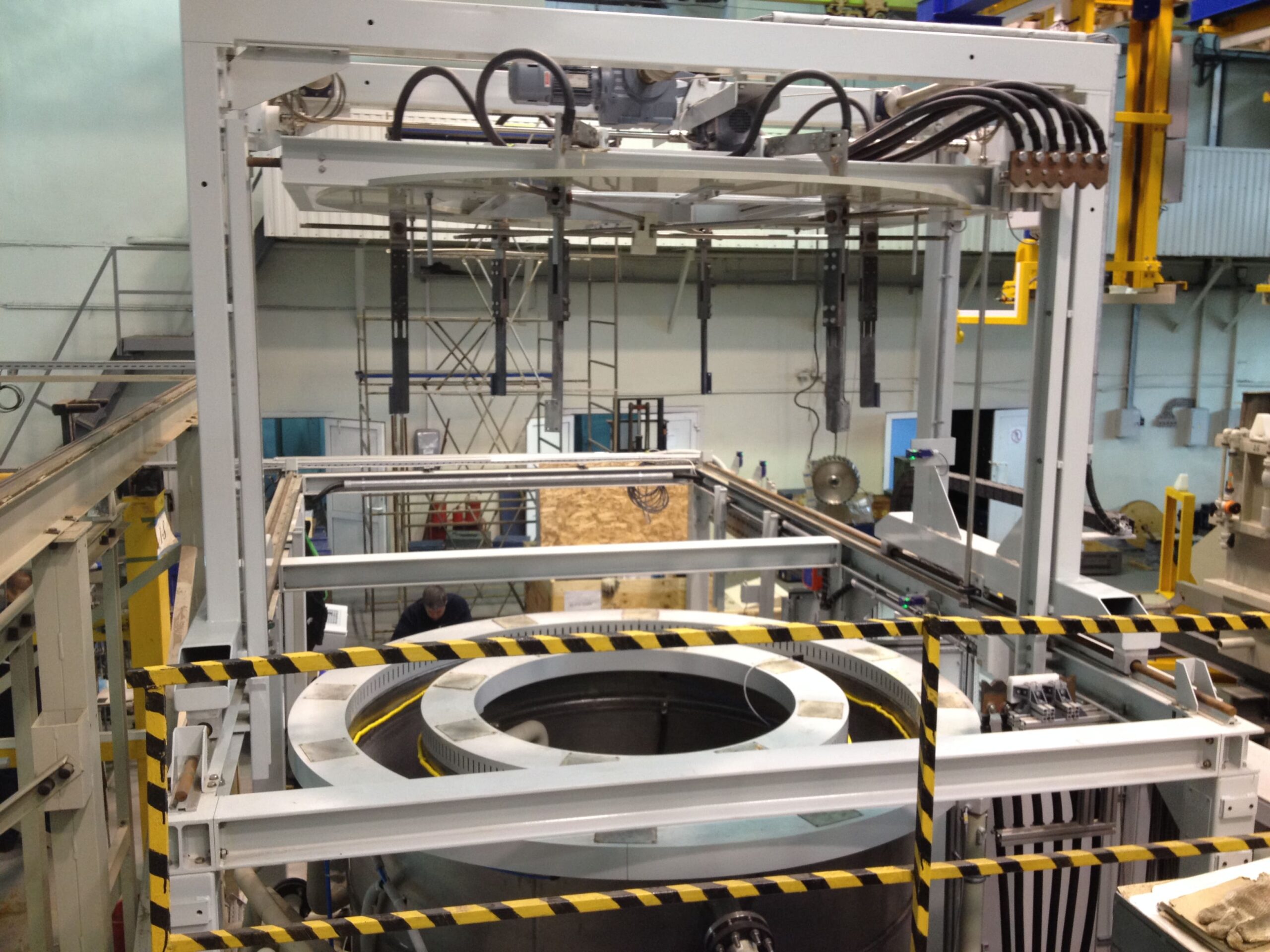
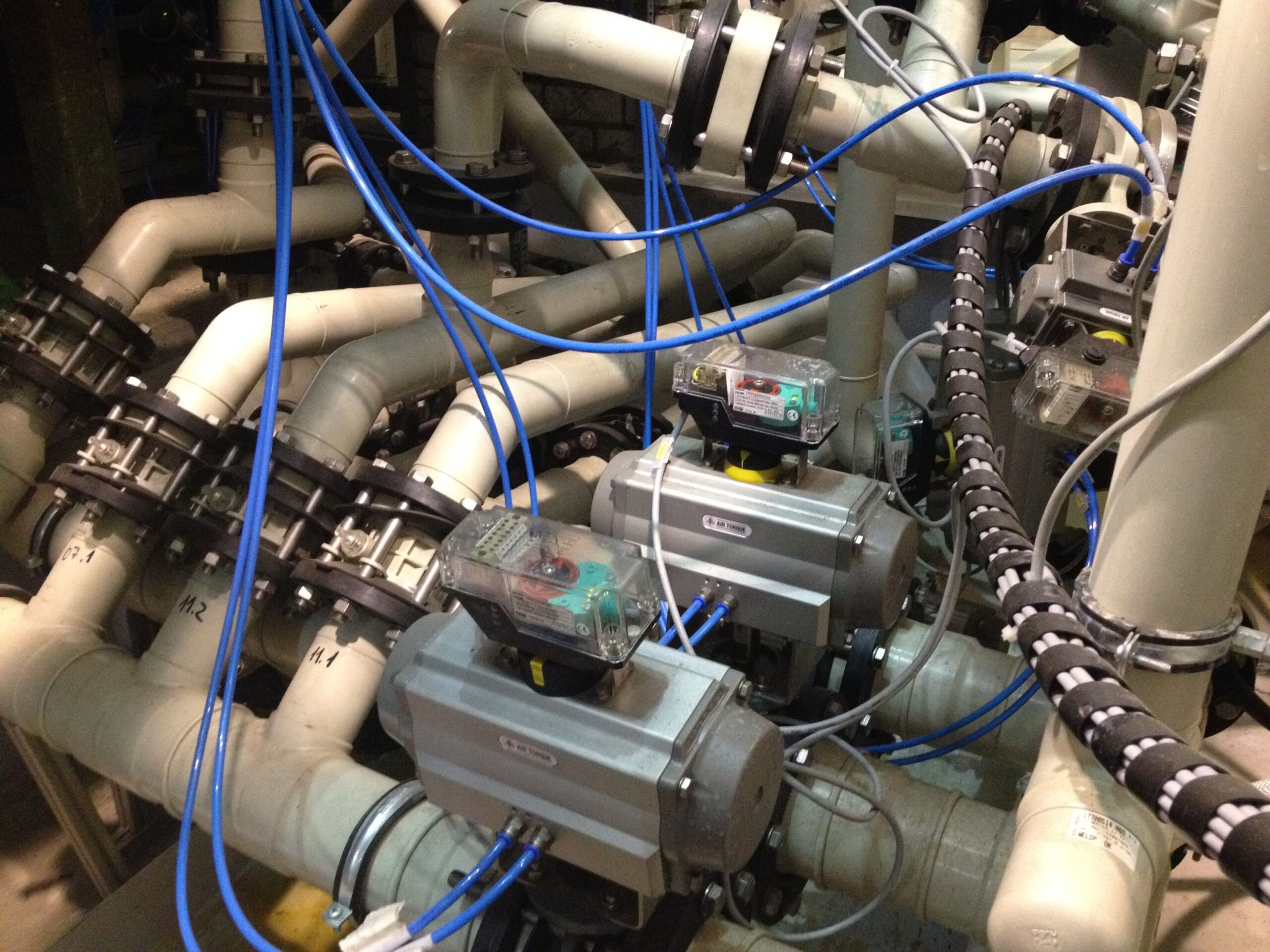
- New process for processing workpieces made of different materials
- Material quality is not changed for the first time
- There are no cracks in the material
- Inductive heating process
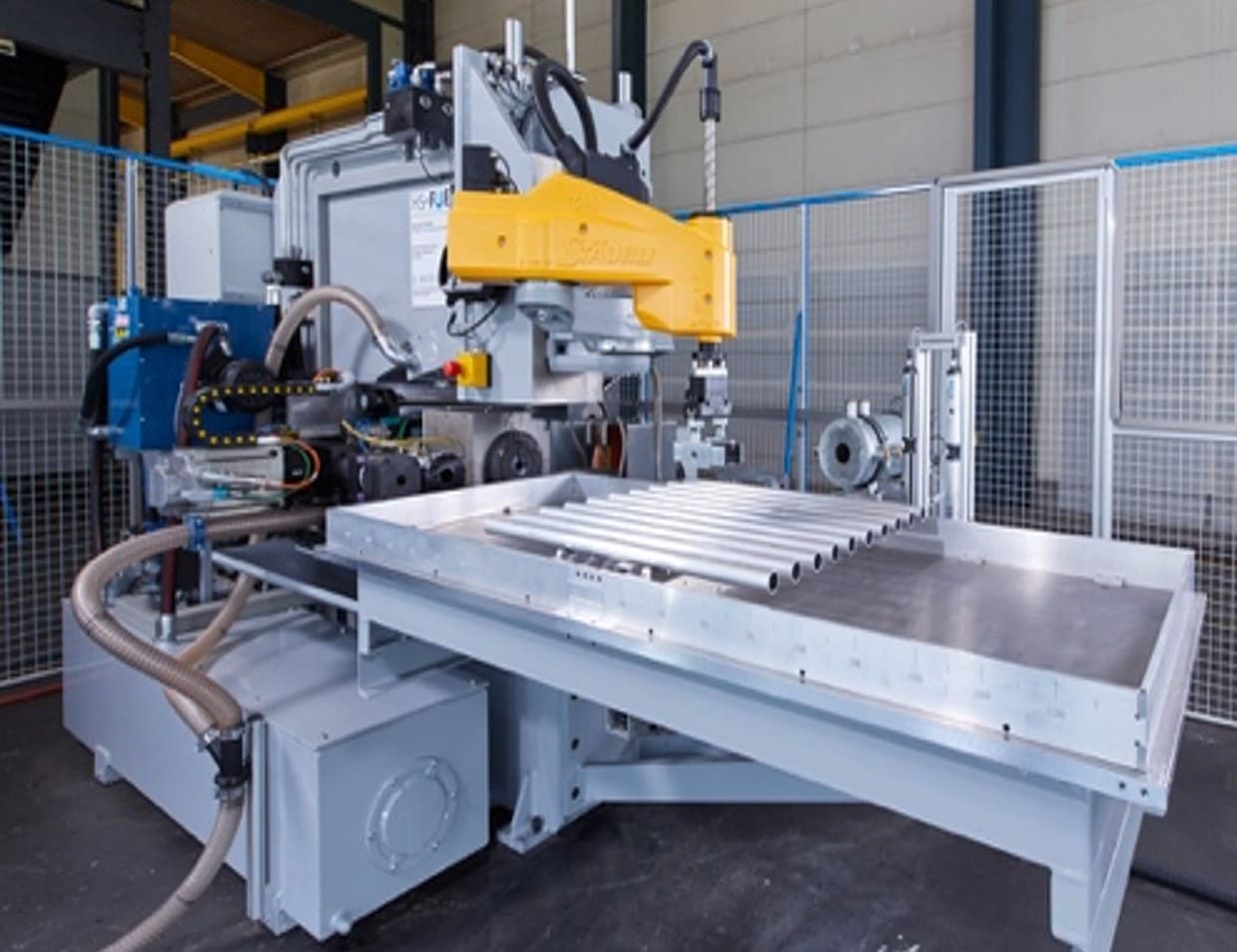
- New laser welding process
- 4m long components with a 60° joint angle and 6mm thickness are laser welded
- No thermal processing necessary
- Material of special quality
- Accuracy when rolling in µ range
- Repeatability in µ range
- Cycle time optimized
- Surface hardened by „rolling“.
- Elongation of the material 1000%
- Automatic measurement with rest system
- Fully automatic gluing on stop with wall thickness of 0.6 mm
- Automatic control of the nates on transparent material
circular M
and Partners

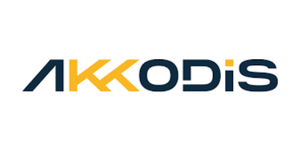
Annett Schulze
Regional Director
Germany North – East
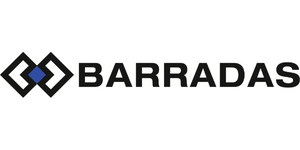
Björn Hötger
CSSO / Chief Strategy and Sales Officer
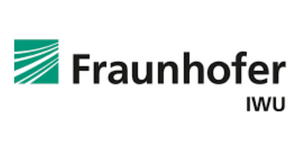
Dr. Thomas Hipke
Head of Lightweight Construction, Textile technologies and circular economy
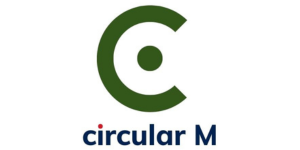
Alexander Feth
CEO & Co-Founder
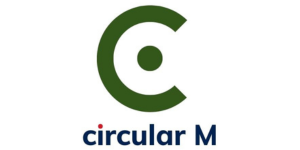
Harry Schaaf
CTO & Co-Founder
contact us
Get In Touch

Address
Beckerstrasse 13
09120 Chemnitz

info@circular-m.com
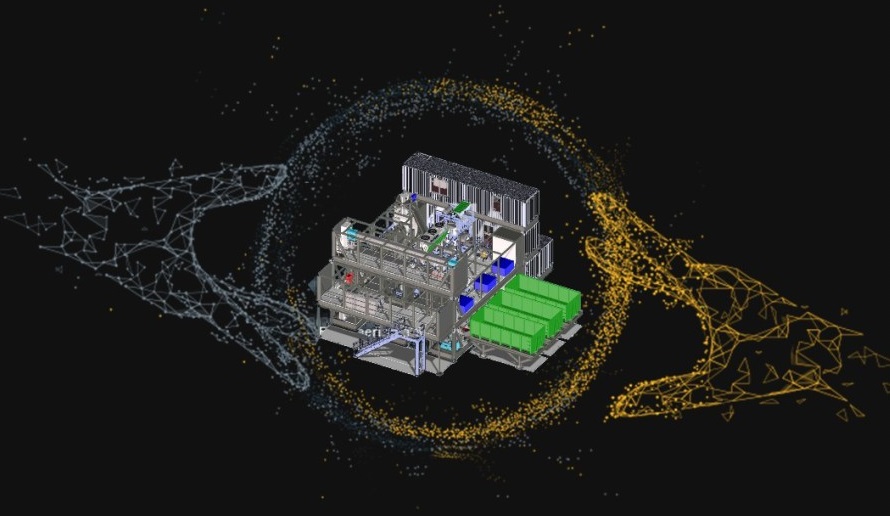
Fire & Water World „Thermolysis“
Fire World 1
Furnace Here you have temperatures up to 1,200°C. Usually you have hardly any critical and almost pressureless atmospheres. Calcination, hardening or swelling processes usually take place in an oxygen-rich flue gas. As a rule, only mechanical properties at high temperatures need to be taken into account. Here, one falls back on proven materials and knows the application limits from practical experience. Typical strengths are in the range of 10 – 20 N/mm².
Water World 2 Chemical plant
First of all, there is a risk to health and the environment. The materials to be treated are basically dangerous, i.e. there is a comprehensive set of rules that the engineer must know and apply. The typical operating temperatures are <500°C and the pressures are >0.5 bar. Here, according to the regulations, it is decisive whether the engineer may calculate with 670 or 550 or only 430 N/mm². Depending on the load case, safeties beyond 2.0 are then required. For a classification as a potentially explosive area, „permanently technically tight flange connections“ are decisive and thus over a cost increase by a factor of 2 to 3 times.
World 1 Engineer is Designer
It is seen what has worked and what has not. Experience counts. Perhaps in the course of time one has created a few Excel tools with which engineering calculations are made according to Roloff-Mateck. If the safety is above 1.3, you feel safe. That’s it …
World 2 Engineer is Paragraph Connoisseur
First of all, the engineer has to know according to which regulation the calculation is allowed. For this purpose, hundreds of pages of rules and regulations are searched for the appropriate passages and exceptions, since the engineer must first assume that he will be held liable in the event of a terrible accident. The Seveso dioxin or the Beirut explosion are always in the back of the mind. So: it’s always better to add a little more safety to avoid triggering an explosion!
World 1 Manufacturing: Kiln Builder
Pyrolysis Kiln for Lignite 2005
Typical are the small companies with less than 10 employees. Manual labour is in demand here. Skill is time and money! Paperwork is a nuisance if you have to do it yourself or expensive „useless stuff“ if you have to hire extra staff for it. In the end, the stove builder is happy when he can deliver another masterpiece of craftsmanship.
World 2 Manufacturing: Chemical Plant Construction
Here a large order is chopped up and broken down into small individual parts. The programmer for a milling programme is happy when he has programmed the programme a little faster than the default. The CNC milling cutter is happy when the part is finished just in time, so that he doesn’t get in trouble with the foreman. The welder enjoys the perfect seam, but does not know what his part is for. The project coordinator is still accompanied by the assistant to put the whole work together. The inspection department watches over everything with a plethora of inspection records to ensure that no defect is detectable in the finished product.
World 1+ Conventional Rotary Kiln Pyrolysis
Now high temperatures, low strength and a critical gas come together in a #rotarykiln. Errors here also lead to major hazards! However, if you know a few basic things, the risk becomes manageable. So the hot #pyrolysis gas is burnt as quickly as possible and thus becomes non-critical, and the risk world is back in order.
World 2+ Thermolysis
Condensation Unit Herne 2010
Here, substances are heated at up to 400°C and thus liquefied. This produces flammable gases. Contained moisture can evaporate abruptly and increase the volume by a factor of 1000. All the alarm bells ring in the engineer’s ears and the fear is immediate: „How can I protect myself? What regulations apply?“ Since you stay below 500 °C, you can now calculate in familiar territory according to the Pressure Equipment Directive.
World 1+2 Rotary kiln thermolysis
The daredevil goes up to process temperatures of up to 900 °C and also combines this gas world with condensation, i.e. flammable liquids, in one system! The front part of the rotary kiln cannot be calculated in accordance with the Pressure Equipment Directive and the rear condensation part requires precisely these regulations! An apparently insoluble task…
Expert on the Major Accidents Ordinance
This expert in paragraphs knows where and which regulations apply to which substances. A conversation with him shows that with smaller quantities, the risks become so small that they can even become negligible. The rule here is: the larger, the more dangerous! Now it is necessary to find the balance between risk fear and factual calculation. If this person is solution-oriented, then something great can come of it!
Project Manager RotaryKiln Thermolysis
This is the person who loves the balancing act and masters these fire-water worlds. He is not a friend of gigantomania like „bigger, faster, more … profit (=risk)“. Practical experience is crucial here! If one’s own experience is not available, then the experience of the old people is necessary who had to deal with such plants 20 or 30 years ago. They have experienced everything that can go wrong and how to counteract it.
Kiln Failure at 1,400 °C „Dragon Baby“
Reality As a rule, a management decides in which world one wants to feel comfortable. The bigger a company gets, the smaller the risks have to be, the more likely one will hear a „Yes, but…“ and a production request will be gratefully rejected. The companies that could build such a 2-world plant are usually too small for projects that can run into the 2-digit million range.
Conclusion
A combination of experienced engineering team, bold 2-world specialist fabricator and risk-averse general contractor / #investor is a combination where everyone can stay in their beloved world 🙂